Defects and Correction Methods of Stainless Steel Sheet Re-rolling
Defects and correction methods of stainless steel sheet re-rolling
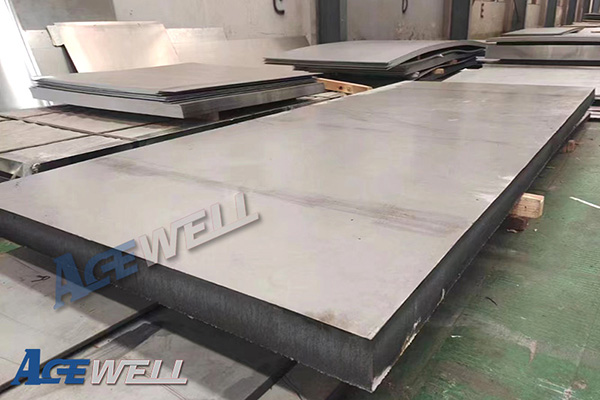
Austenitic decorative stainless steel plates are characterized by their toughness, strength, viscosity and cold hardening. The degree of deformation is continuously increasing during the rerolling process. This type of stainless-steel plate undergoes a continuous transformation from austenite to martensite. The rolling-forming of stainless sheets is also made difficult by this. Stainless steel rerolling defects can include wrinkles as well as scars, breaks, and cracks.
wrinkle defect
Flange wrinkles
When the stainless steel sheet passes through the mold, the flange part is not only affected by the blank holder force, but also is affected by radial tensile stress and tangential tensile stress. When the tangential compressive stress is large, the flange part of the sheet may undergo plastic instability and tangential bending, causing the flange part of the stainless steel sheet to produce slight waves in the vertical direction, that is, flange wrinkling. The main reason for the formation of flange wrinkles is that the blank holder force is too small and the die fillet radius is inappropriate.
The outer edge of the sheet becomes thicker when the blank holder force, in both the vertical and rounded directions, is too small. This is due to the compressive and radial tension forces. When the stainless steel sheet re-rolls, wrinkles will appear. Rolling bars can be used to fix the problem. The blank holder force may also be adjusted.
The quality of the finished piece is directly affected by the size of the fillet. This will influence the internal stress and size of blank holder force required, wrinkle formation, wall thickness thinning, and number of rolling cycles. The greater the internal stresses generated by the stainless sheet, the larger the blank holder forces, and the worse the wrinkles on the rolled piece. The greater the radius of the filled, the lower the blank holder force required, the less pressure the stainless steel sheet has, and the greater the range of compressive forces in circumferential directions. The rounded corners of the sheet should be ground down to smoothen the surface and prevent wrinkles.
wall wrinkles
The cylinder walls are the main cause of wall wrinkles in the re-rolled stainless steel sheets. Correcting the problem is as simple as adjusting the rerolling gap and applying tension perpendicularly to the rerolling direction.
scars
Change Rolling Scar
The re-rolled stainless sheet may show small slip marks, or scratches, when it passes through the rounded corners of the die. This defect will get worse as it progresses because the rounded corners of the die are the places where the sheet has the most deformation force. The product will be scratched and the smoothness will be affected. Scratches, pitting, dents, etc. Also, the surfaces of the concave and punch molds will show scratches, pitting and dents. The problem can be solved by chromium-plating the punch, adjusting rolling gap and using suitable lubricants.
Mold scratches
Scratches are often caused by bright spots that appear on the surface of a product when the surface roughness and fillet of a punch and die do not meet the required requirements. Mold modification is usually the best way to fix this type of defect.
Cracks and Breaks
Bottom Dropped
Cracking on the bottom is a very common problem when re-rolling. It can be avoided by increasing the fillet diameter of the convex die and concave blank, reducing the force of the anti-wrinkle blank holders, strengthening lubrication and finishing machining, re-rolling and the surface of the work die.
sunken bottom
The bottom of the product will be sunken if the residual stress is present after the processing. This is because the piece is not cracked yet, but it is necked by the re-rolling. The method of correction is to adjust fillet radius on the concave and convex molds in order to maintain a reasonable state of stress during the rolling process.
Solution
Selection and use of lubricants
There are two important factors to take into consideration when selecting lubricants. The lubricant should have a relative thermal stability, and provide lubrication even when heated.
Second, even when the temperature increases at the time of rolling, lubricant will adhere to the surface of both the roughness and mold evenly without forming an accumulation or thick film.