Problems and Solutions in Stretching Stainless Steel Plates
Problems and Solutions in Stretching Stainless Steel Plates
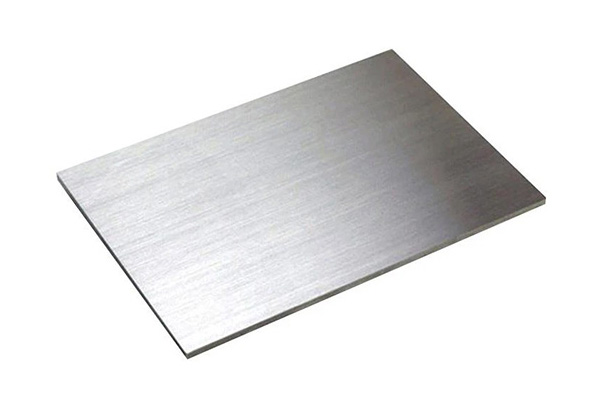
The stainless steel products are popular due to their beautiful surface, excellent corrosion resistance, high-temperature oxidation resistance, and high-and low-temperature strength. They are used widely in kitchen utensils and light industry, as well as for decoration. The stamping performance of stainless steel is not good. Its surface is easily scratched and the molds are prone to tumors. This has a negative impact on the quality and efficiency of production. To improve the quality of the parts and the mold life during the stamping, it is necessary to start with the mold structure, the mold materials, the heat treatment, and the lubrication.
Characteristics of stainless steel sheet stamping
(1) High yield point, high hardness, significant cold work hardening effect, and prone to defects such as cracks.
(2) Thermal conductivity is worse than ordinary carbon steel, resulting in large deformation force, punching force, and tensile force.
(3) The plastic deformation is severe and hardening during deep drawing, and the thin plate is easy to wrinkle or fall off during deep drawing.
(4) The deep drawing mold is prone to bonding tumors, resulting in serious scratches on the outer diameter of the part.
(5) When drawing, it is difficult to achieve the expected shape.
Solution
Selection of materials and heat treatment of mold working parts
The best way to solve the sticking problem is by choosing a mold material that has a good affinity with the stainless steel sheet. Attention should be given to two points. It is important to choose a material that has a high level of anti-adhesion and wear resistance, as well as friction reduction. The use of cast aluminum and duralumin has better anti-sticking effects. Die made from tungsten carbide steel-bonded carbide have a life that is many times longer than dies made from Cr12Mov Soft Nitriding. Cemented carbide inserts are also used to strengthen the weaker parts of the mold. This will give it excellent wear resistance, long-lasting surface roughness, and a good size control. It is expensive and therefore rarely used.
Surface treatment of the working part
Surface quality is very important for stainless steel drawing dies. Surface roughness that is lower can reduce friction, and increase adhesion resistance. It is important to remove the processing marks after the drawing die has been ground. In the manufacture of molds, it is often overlooked that grinding and polishing are important processes. Note this. The polishing and the grinding of the mold should make up one third of the total mold processing. This is because the quality of stainless steel products is largely determined by the polishing technology and the grinding technique of the mold. Surface roughness is reduced and mold grinding time is reduced. The service life is also improved. The surface of the mould is not sufficiently polished and the stainless sheet is drawn deep, it's easy to cause bonding tumors. This will result in serious scratches on the drawn product. Polishing the scratches is a time-consuming process and not very effective. We should therefore put in a lot more effort to polish the mold. We can only reduce scratches on products by improving the accuracy of surface processing of the mould.
China has developed a number of new polishing techniques and tools in recent years. There have been new technologies and equipments developed, such as electrolytic polishing and ultrasonic wave. Information indicates that electrochemical polishing experiments were conducted on three types of molds: CrWMo (Cr-Mo), 3Cr12W8V (Cr-12), and Cr12. This type of polishing was able to change the surface roughness from Ra3.2-Ra1.6 of the mold's cavity in just 5-10 minutes. Based on reducing Ra0.4-RaO.2. Electrochemical polishing can also be used to increase the hardness of the surface, which will improve the wear resistance. Another example is the use of an ultrasonic machine for fine polishing the cavity after nitrocarburizing. This can help avoid the problem that manual polishing can easily damage the nitride layer. It is important to actively utilize and summarize the latest polishing technologies.
Lubrication during processing
The deep drawing properties of stainless steel show that the formation of tumors is caused by the direct contact of the sheet with the mold. Theoretically, this is an undisputed fact. The lubricating layer in the middle is not broken and functions as a lubricant throughout. The basic criteria for choosing lubricants is "anti-sticking and reduction of friction".
In general, lubricants that contain extreme pressure additives or solid lubricants will produce better results. It is to increase the ability of the lubricant to lubricate metallic surfaces. This is done by producing compounds that contain sulfur, phosphorus and chlorine, which react chemically at high temperatures with the metal surface to create iron sulfide or ferric chloride. To increase the adsorption and strengthen the oil film. Better lubricate surface of mold and product. Lubricants may also include synthetic grease, soap, mineral oils, fats, or synthetic grease. These lubricants have better effects on shallow drawing stainless steel. Shallow drawing can be done with organic mineral oils that contain water-soluble emulsions or are diluted in oil.